Understanding Material until Failure
The mechanical description of continuous fiber-reinforced thermoplastic composites is challenging. On the one hand, the mechanically non-linear, orthotropic material behavior requires the characterization of a total of five material functions to fully describe the stress-strain behavior. On the other hand, the failure behavior is strongly dependent on the respective stress state and the interaction of individual stress components, which makes modeling even more difficult.
To fully exploit the immense potential of these materials in practice, we pursue the following approach:
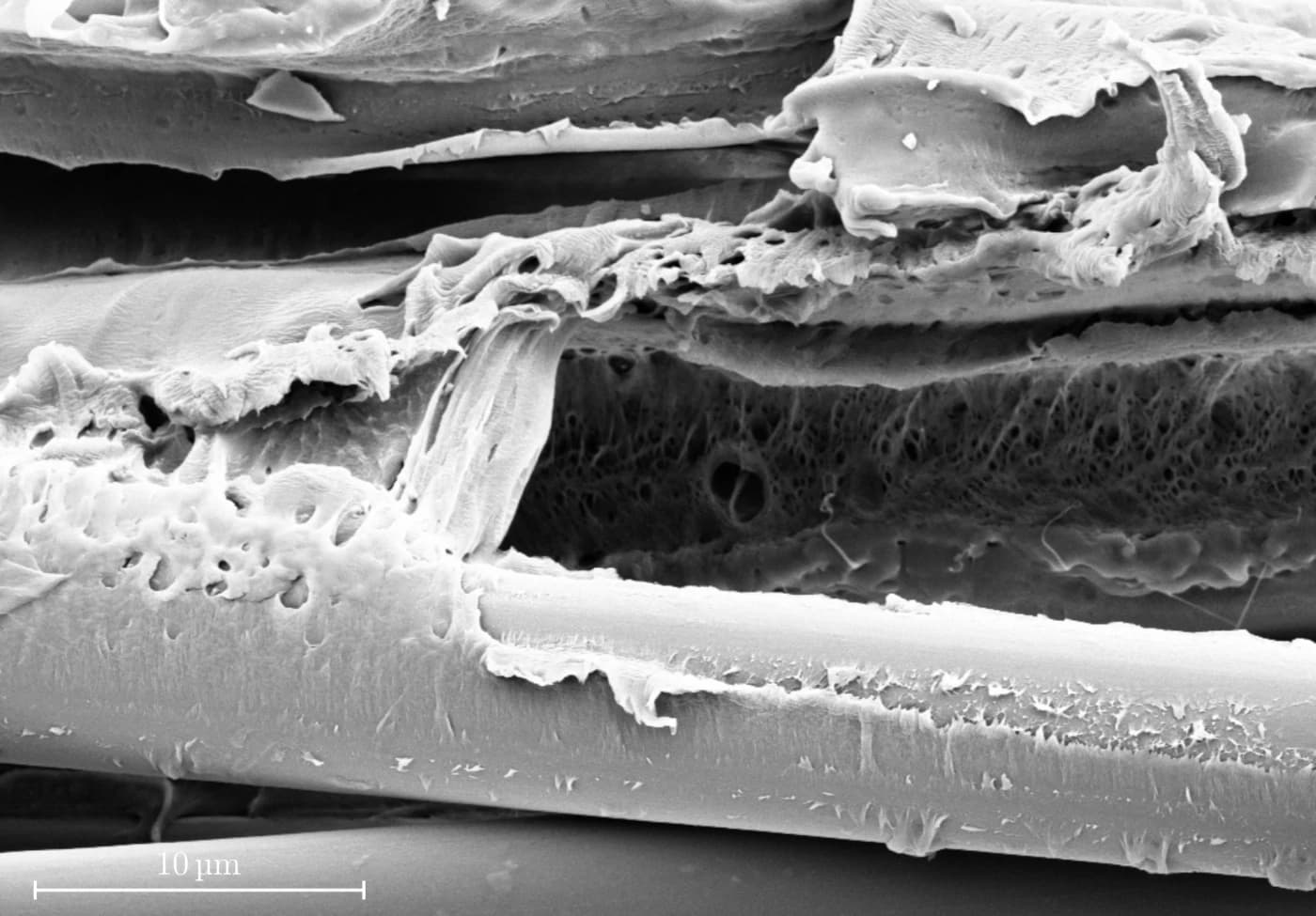
Experimental Characterization
The exact characterization of the mechanical material behavior is crucial for the efficient component design of fiber-reinforced plastic composites. The selection and application of suitable experimental methods for determining the material characteristics is of particular importance. In contrast to metallic materials such as steel or aluminum, for which two characteristic values (modulus of elasticity and transverse contraction coefficient) are usually sufficient, a total of four characteristic values must be determined for fiber-plastic composites in the plane stress state and even five in the general stress state. This requires the use of multi-axis testing techniques in combination with precise measurement methods, such as optical strain measurement.
We implement precisely this approach for our materials and thus create a basis for systematically exploiting their full mechanical potential in the application.
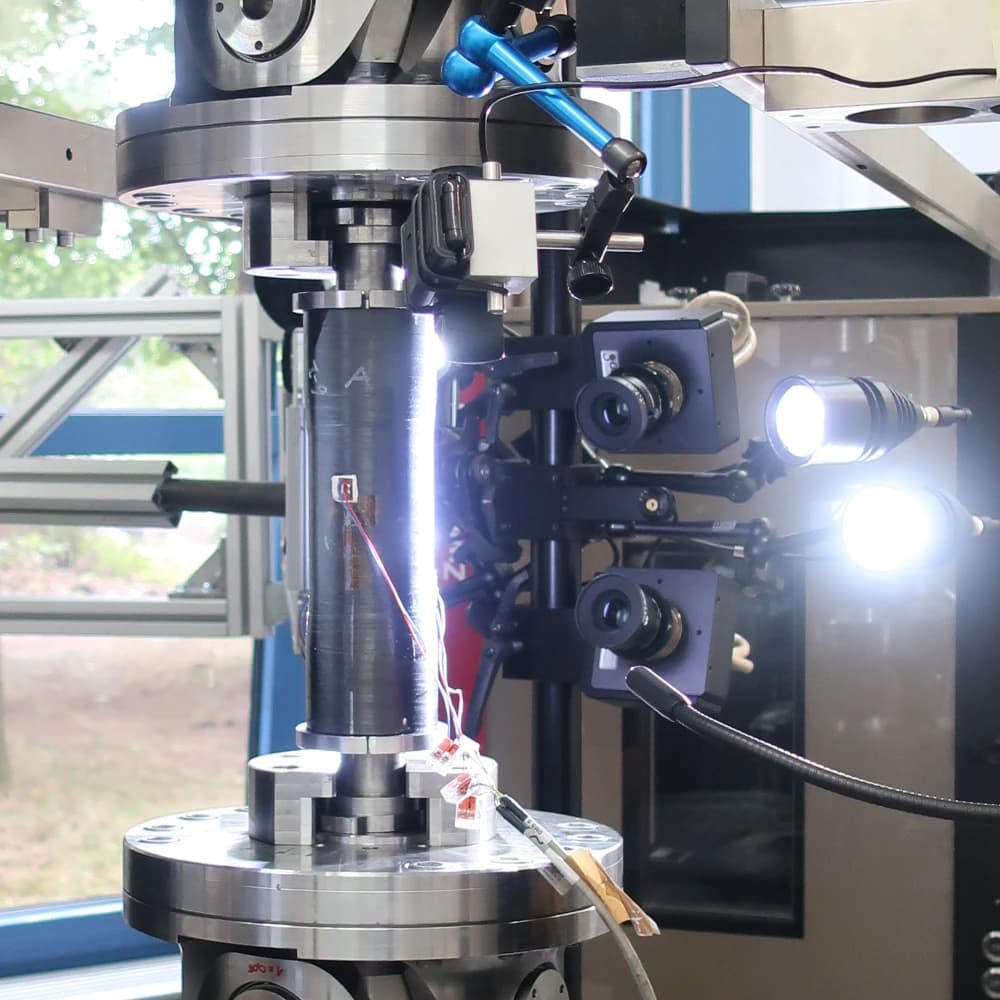
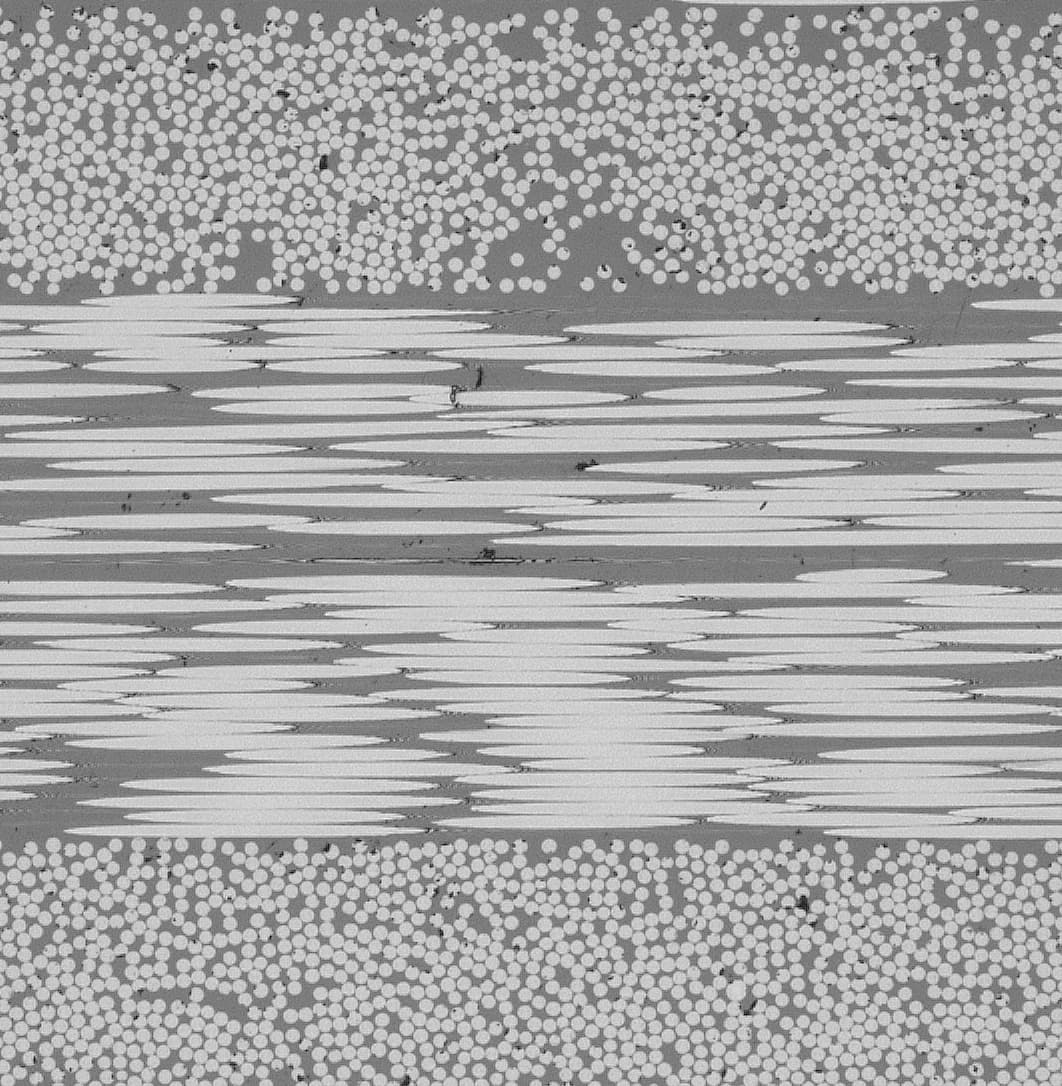
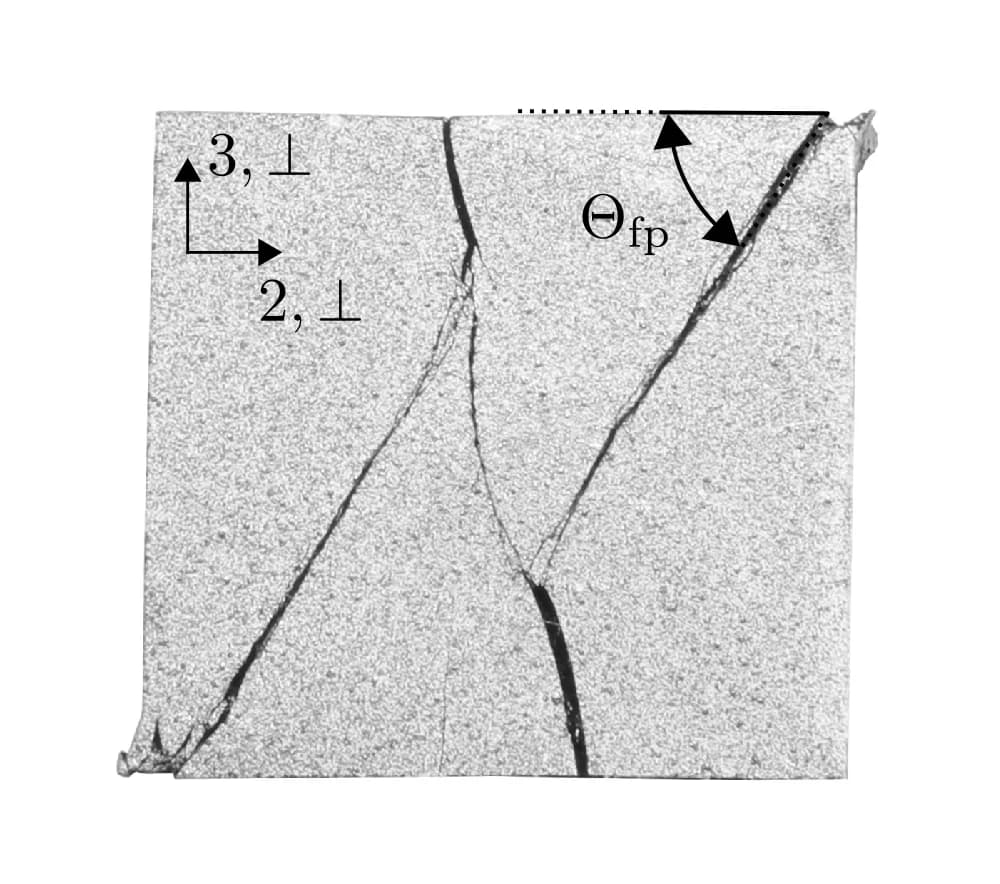
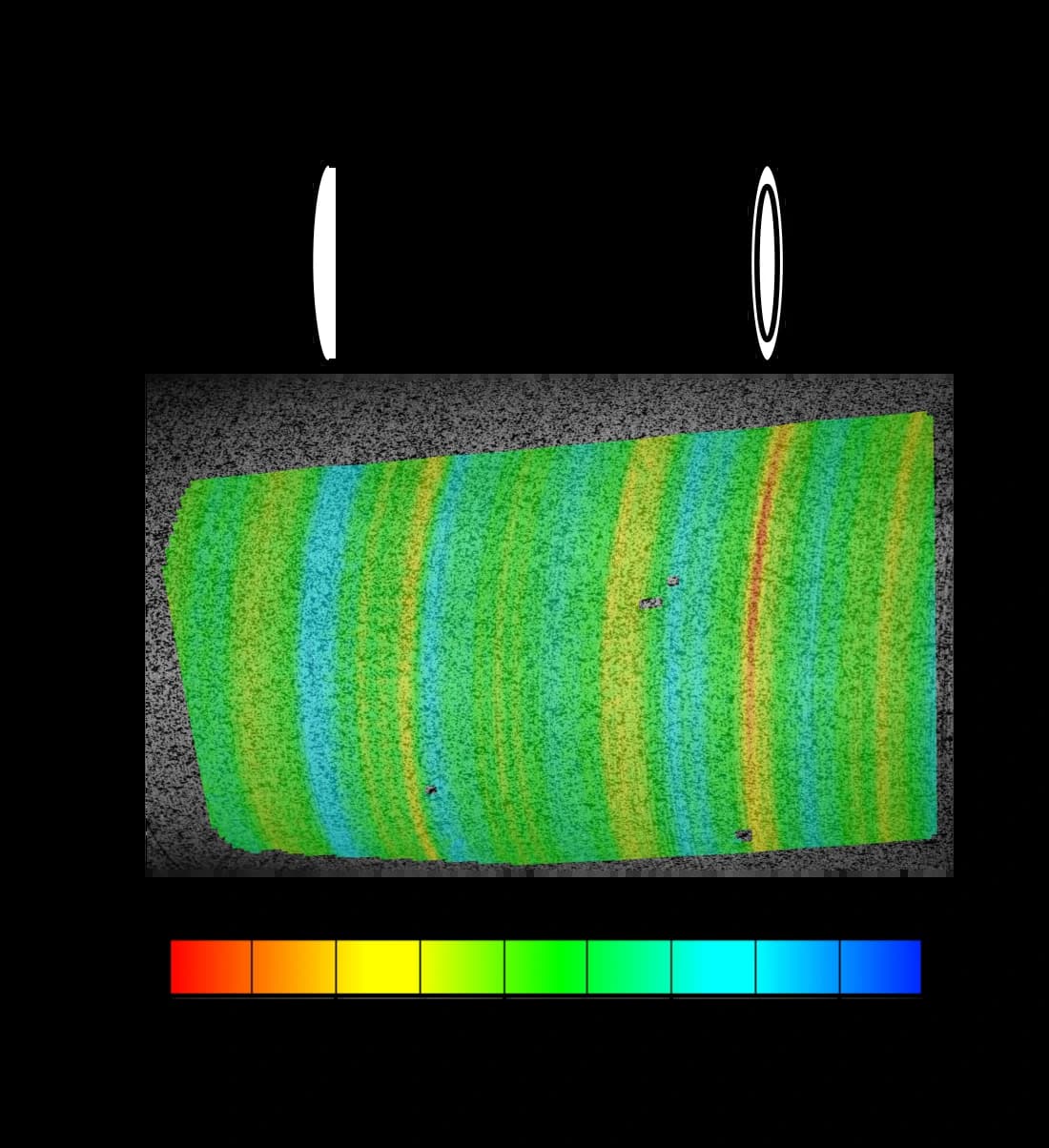
Material Modeling Based on Our Own Database
Fracture Curve of Carbon-Fiber Reinforced Polyamide 6 (CFPA6) in In-Plane Stress
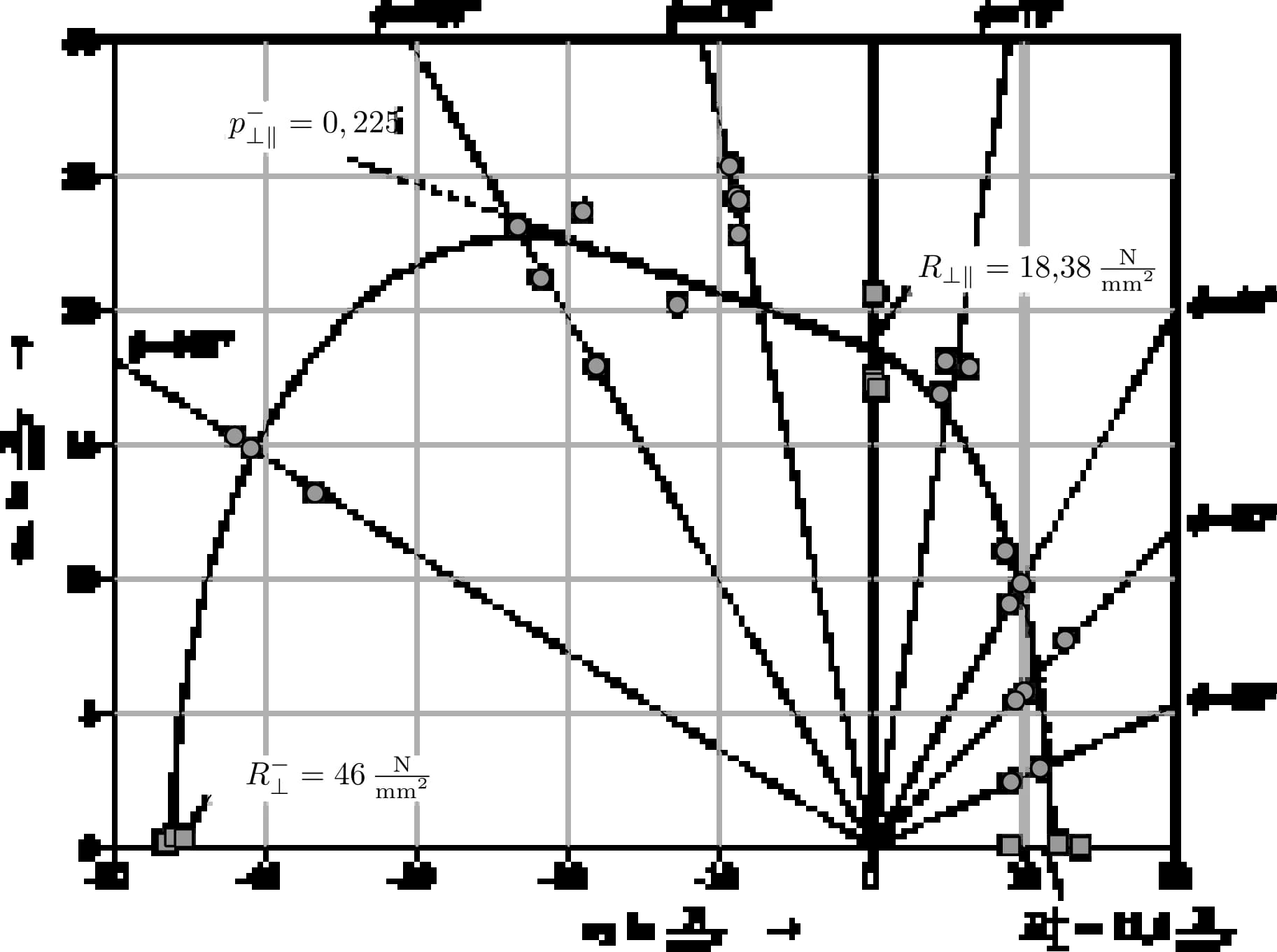
The determined material characteristics must be made usable in practice for engineers and component designers. A particular challenge lies in the description of the failure mechanisms, as fiber-reinforced plastics can exhibit different failure modes resulting from stress interaction.
To this end, we have developed our own material model that enables a non-linear description of continuous fiber-reinforced plastics and integrates a suitable failure model. This gives us a simple and effective approach to designing highly stressed components based on our materials.
Our model is based on the results of several years of research by the Leibniz-Institute for Composite Materials (leibniz-ivw.de). In close cooperation with the institute, we continuously adapt the modeling to our new materials.
Composite Specific Component Design
Our materials have enormous potential-provided they are used in a targeted and suitable manner. Due to their direction-dependent mechanical behavior, components made from composites require specific design principles. Areas where loads are applied and zones where stability is at risk are particularly critical. Targeted design adjustments can achieve an economical, functional and material-specific design.
Simply substituting conventional metal components with composite parts does not usually lead to the desired results.
As designer and producer of these materials, we have in-depth expertise and support you in exploiting their full potential for your application in a target-oriented way-on request also through FEA-supported design and analysis. For this purpose, we use our own material model, specially developed for the non-linear description and failure behavior of our fiber thermoplastic composites.
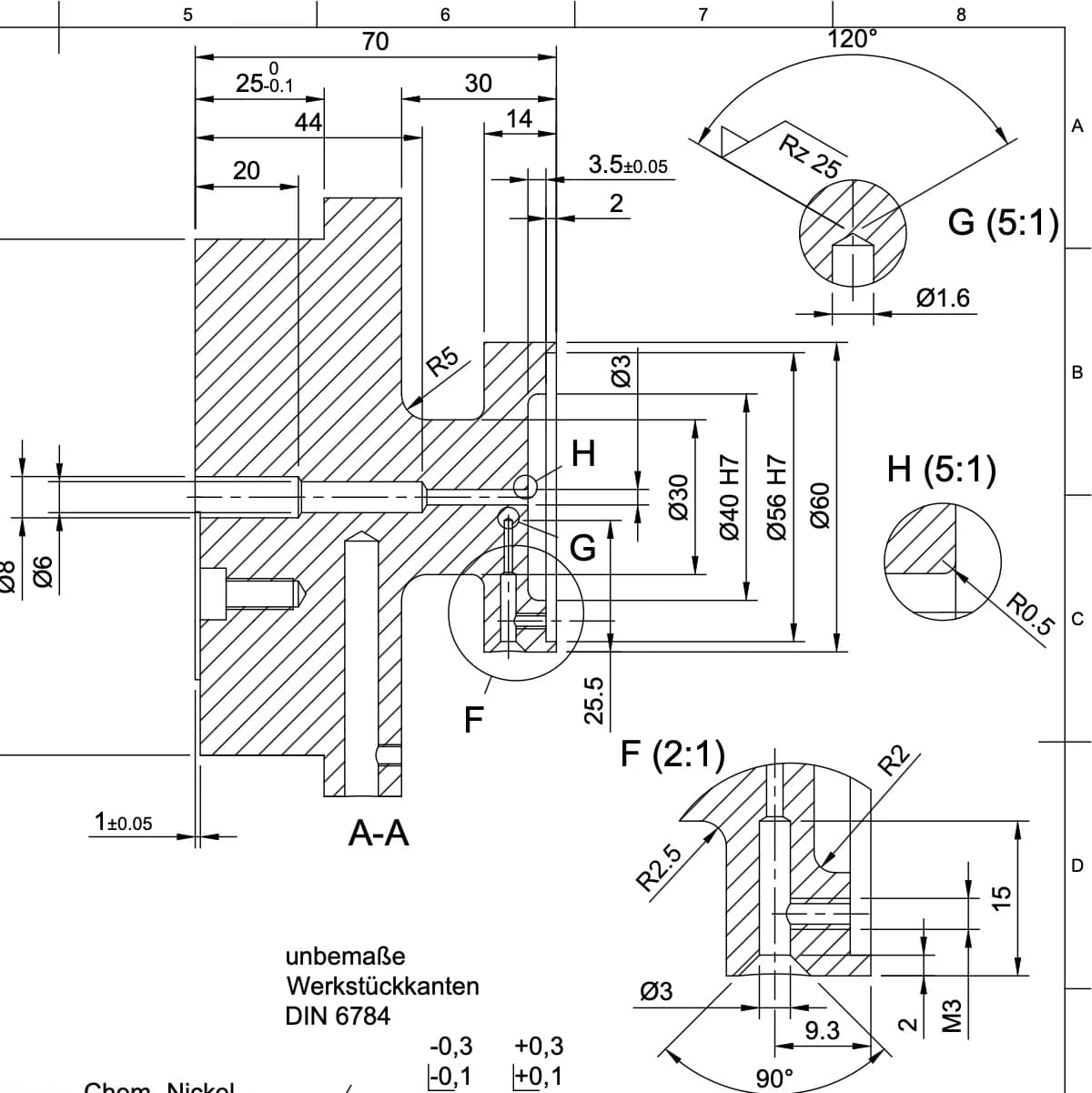
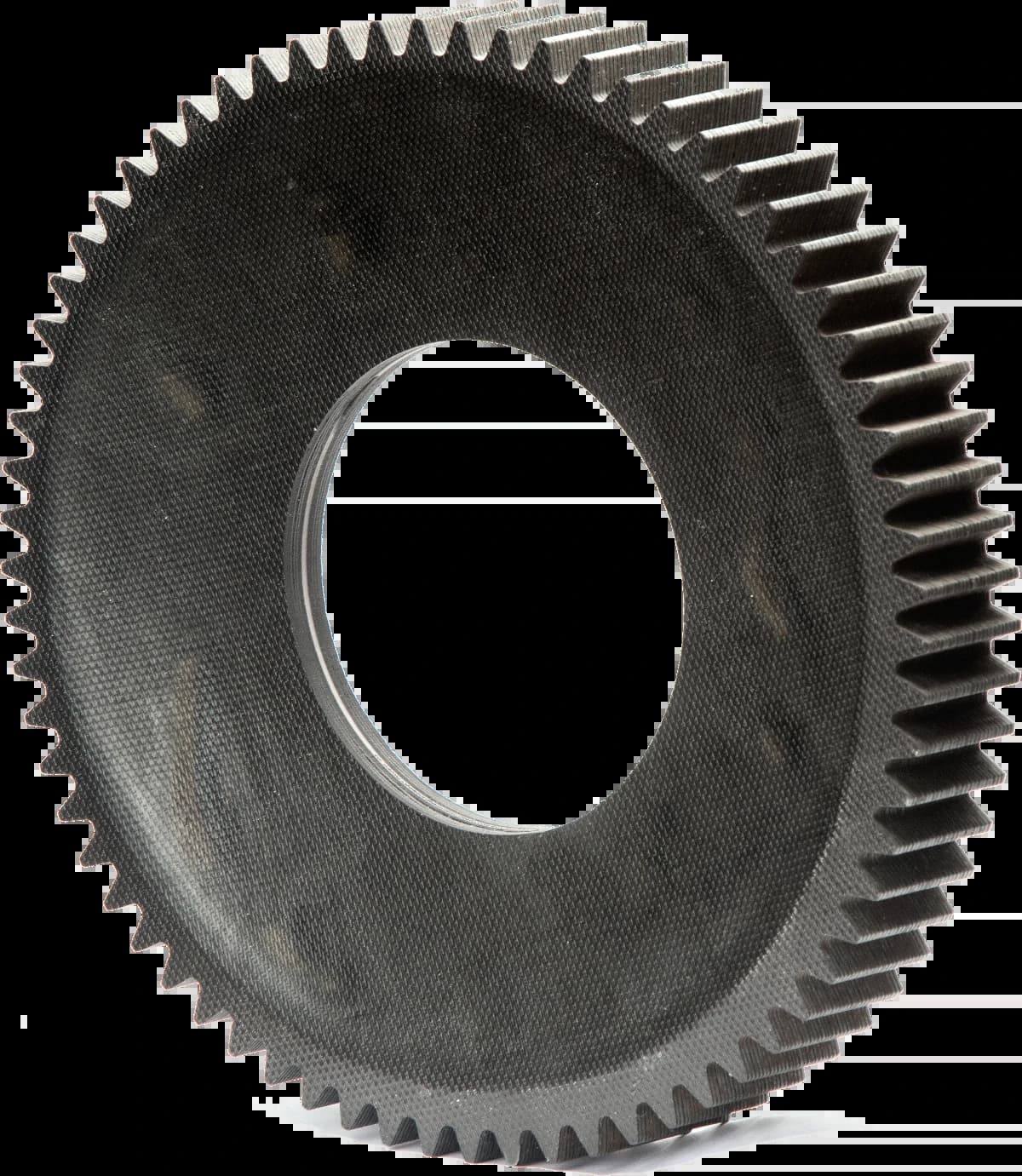
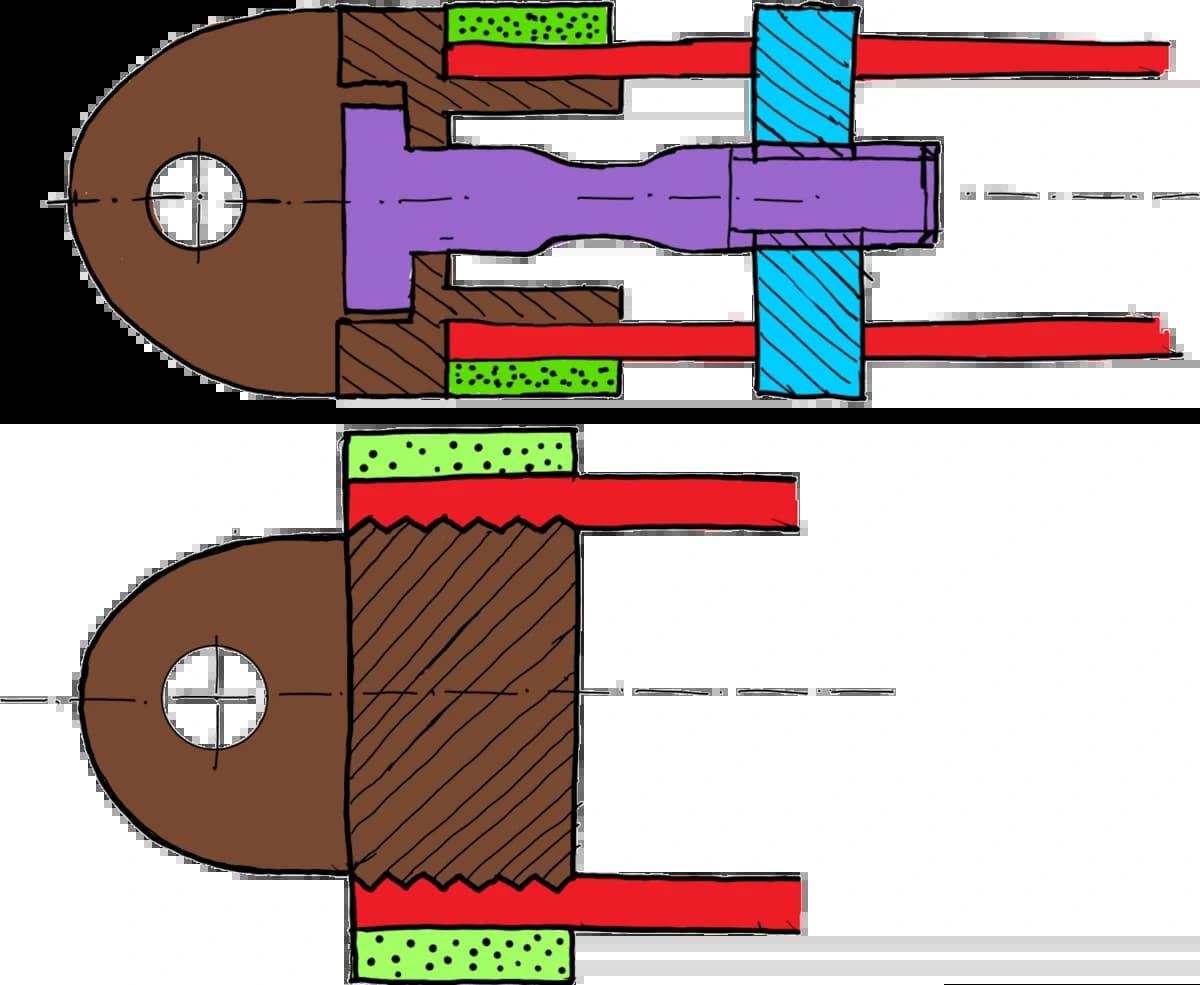
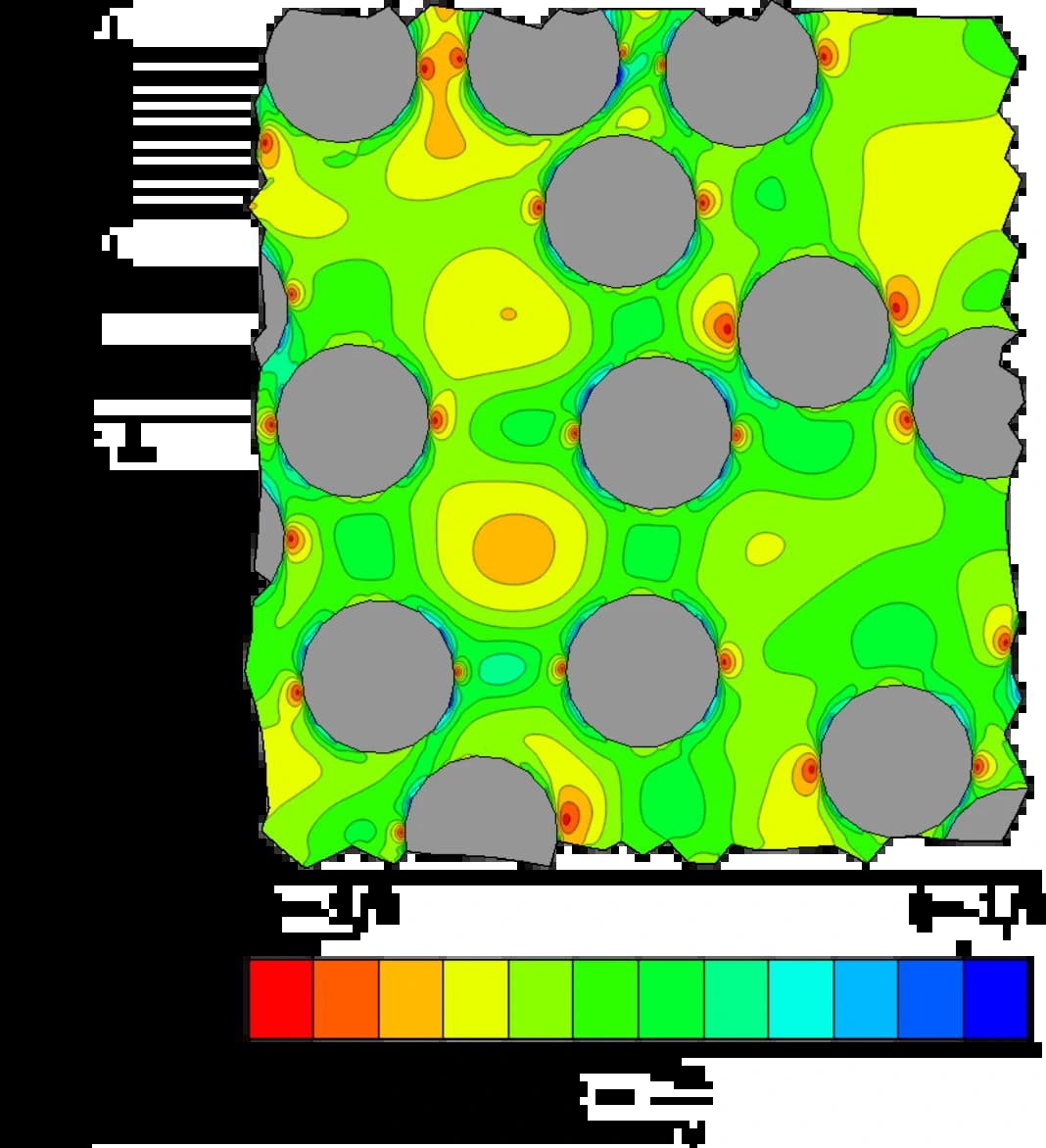